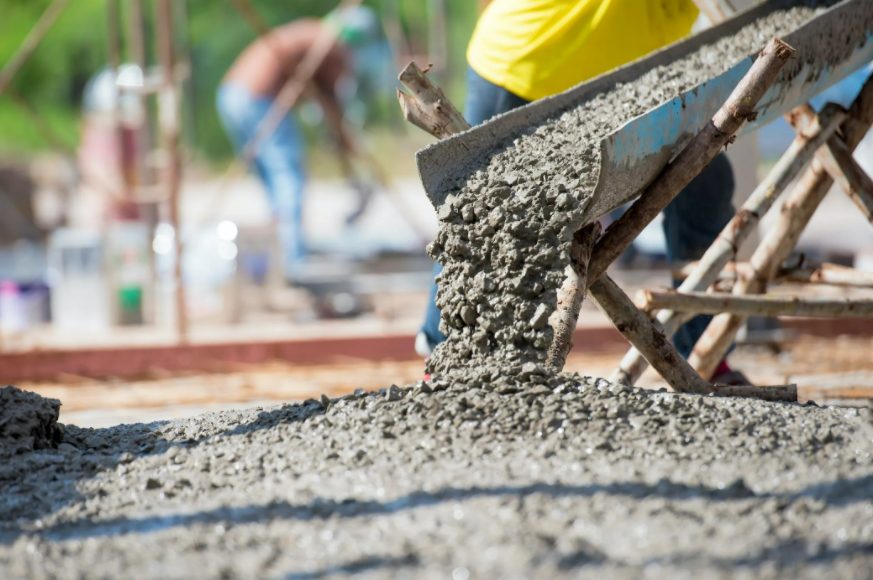
Despite committing to Zero Net Carbon most AREIT Managers are ignoring the embodied carbon emissions in their development projects – the leaders are not.
In the context of the property industry, embodied carbon emissions are those generated during the manufacture, construction, maintenance and demolition of buildings. Few AREITs make reference to embodied carbon emissions in their Sustainability Reports with most not currently reporting them (as part of Scope 3 emissions) given the challenge in capturing data and influencing the results.
Mirvac, for example, don’t count Scope 3 emissions in their commitment to Net Zero Carbon as they claim to have a very low influence over a number of scope 3 emissions, such as how a tenant chooses to operate within a building they’ve leased. Mirvac has however committed to taking action on scope 3 emissions, particular in high impact, high influence areas (but have excluded construction work).
Without action from the development industry to turn to low carbon alternatives, embodied carbon will be responsible for 85 per cent of Australia’s built environment emissions by 2050[i].
When all sources of Green House Gas (GHG) emissions are considered, buildings are responsible for approximately 28% of total emissions[ii]. Of these GHG emissions, 74% come from building operation (Scope 1 & 2 – heating, cooling, lighting, etc.), with the remaining 26% embodied in construction products, materials, and construction processes (Scope 3)[iii] .
Like Mirvac, most Investment Managers are turning their attention to reducing GHG emissions in the management and operation of our buildings via improvements to NABERS ratings, Green Star Certifications and commitments to Zero Carbon however the far less attention is given to the emissions generated from in the construction and development processes.
If Australia reduced the embodied emissions in new commercial and residential buildings by just 10 per cent between now and 2050, this would eliminate at least 63.5 megatonnes of emissions – the equivalent to taking 13.8 million cars from the roads for a year.
The report released in July 2021 from the GBCA “Embodied Carbon & Embodied Energy in Australia’s Buildings “ finds that embodied carbon – the emissions generated during the manufacture, construction, maintenance and demolition of buildings – made up 16 per cent of Australia’s built environment emissions in 2019 and that without intervention this share will balloon to 85 by 2050.
GBCA’s Chief Executive Officer, Davina Rooney said “While we are making great strides forward in our work to tackle operational carbon in buildings, embodied carbon is largely locked in before a building is occupied. The decisions we make today will have implications and impacts for decades to come.”
“As Australia’s electricity grid decarbonises, and as more buildings are powered by renewable energy, embodied carbon from the built environment will make up a greater proportion of Australia’s total carbon footprint – increasing by 50 per cent from 2019 to 2050,” says Dr Barbara Nebel, co-author of the report and Chief Executive Officer of thinkstep-anz.
A significant share of embodied emissions in buildings come from common building products, like concrete and steel, that are manufactured through process heat and chemical reactions. This means their embodied emissions will not decrease by decarbonising the electricity grid alone.
The good news is that a 10% reduction in achievable with the adoption of alternative processes and materials.
Cement production is the world’s single biggest industrial cause of carbon pollution, responsible for 8% of global emissions. Portland cement has been the world’s standard cement since the 19th century. The key raw material for Portland cement is limestone, which releases carbon dioxide as it is heated in a cement kiln. This single process accounts for about half of the carbon emissions associated with cement making, with another 4% coming from the energy required to make cement.
One alternative to Portland cement which has the potential to be a zero-emissions product is geopolymer cement, a class of cements usually made from fly ash (a byproduct of coal-fired power stations) and ground-granulated blast-furnace slag (a byproduct of steelmaking) or clay (metakaolin). Holcim EcoPart product is one example of a low carbon cement. Holcim claim that the product can reduce carbon emissions by 30-60% compared to standard cement. Wagners have a similar product which claims a 76% reduction in embodied carbon.
Another strategy is to capture waste carbon dioxide from the cement manufacturing process and to chemically seal it within rock. Unlike conventional carbon capture and storage, there is no risk of leaking or need for monitoring post-storage.
Some firms are now using a 50:50 blend of Limestone and Sand but heating it to a lower temperature of about 1200°C rather than 1500 °C, cutting tow sources of carbon dioxide: less limestone and less fossil fuel.
Cement is usually mixed with sand, water and aggregate – rock fragments – to make concrete for construction. The water reacts with the cement, causing it to harden in a process called curing.
The most exciting new process is the use of Carbon Negative Concrete, a process which uses the same above ingredient to make concrete, but uses CO2 rather than water to cure the concrete, effectively storing waste carbon dioxide back into the finished product, and entirely eliminating the carbon emissions.
Other building products and manufacturers are also focused on carbon reduced alternatives, however unlike Cement and Concrete, most other products’ emissions are from the energy used in their production process and will turn to alternative energies to reduce emissions.
BlueScope Steel has achieved a 40% reduction in GHG emissions footprint at their Australian operations since 2005 and has committed to a further 12% reduction in steelmaking GHG emissions intensity by 2030. Likewise, Brickworks and CSR are adopting alternative energies in the production of bricks and pavers.
At this stage, Dexus are committed to assess the embodied carbon in their developments in the next 2 to 7 years, with a view to reducing embodied carbon over time.
Our largest developer, Goodman also do not report embodied carbon emissions and currently have no commitment in place to reduce these emissions in future developments.
Charter Hall are leading the way with a stated commitment to achieve Net Zero upfront carbon emissions (embodied carbon and construction) achieved for all new Office and Retail site developments by FY30 and have piloted this in the development of 2 childcare centres in WA, capturing the data and acquiring Australian Carbon Credit Units to offset the emissions.
We expect other investment managers will follow, and are likely to start with commitments to adopt low carbon materials and to set targets on reducing emissions in new developments by 40%, an objective also established by the Green Building Council of Australia (GBCA).
The Green Star building certification process provides points for reductions in embodied carbon emissions and whilst most existing rating can achieve high ratings without Embodied Carbon points, the GBCA will be adapting their star ratings to incorporate this objective.
For more information on how to tackle embodied energy emission check out our recourse links below or contact the GBCA.
Further Information
- Embodied Carbon in Australia’s Buildings July 2021
- climate-positive-buildings-net-zero-ambitions
- Rethinking Cement Summary 2017
- Mirvacs-Statement-on-Scope-3-Emissions
- Charter-Hall-Sustainability-Report
- DXS-Sustainability-Report
- GPT-Sustinability-Report
Disclaimer: The information contained on this web site is general in nature and does not take into account your personal situation. You should consider whether the information is appropriate to your needs, and where appropriate, seek professional advice from a financial adviser.
- [i] Embodied Carbon & Embodied Energy in Australia’s Buildings
- [ii] (Climate Watch, 2021)
- [iii] (UNEP, 2020)