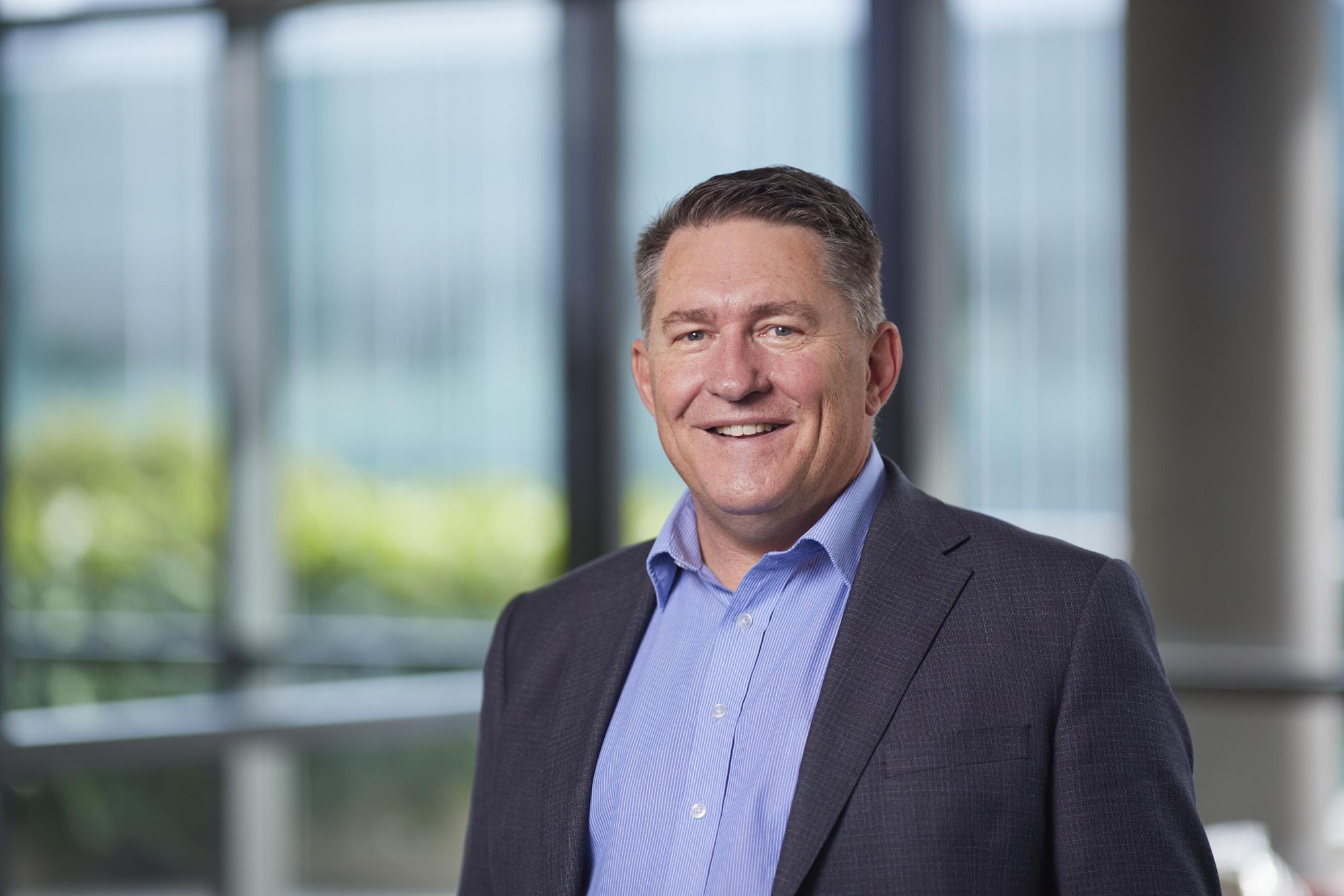
Prological Managing Director Peter Jones discusses how warehouse design has been hamstrung by focusing on square rather than cubic metres, at the cost of proper space utilisation and efficiency – and offers his thoughts on how to unlock benefits through the cubic approach.
In the world of warehouse design, it is common practice to measure and plan using square metres rather than cubic metres. However, this method of measurement may not be the most effective.
The preference for square metres can be traced back to the traditional purchasing process of industrial property, which is based on land measurements. Even when companies vote on the construction of a warehouse, the decision is often based on square metres rather than the actual cubic capacity of the facility.
However, thinking about warehouse design in terms of cubic metres rather than square metres can lead to a more efficient use of space.
As an example, in a typical 10,000 square metre warehouse with a 13-metre roof height, the cubic utilisation is only 17%. By increasing this utilisation to 25%, there is the potential for a 50% increase in the cubic utilisation of the facility.
This highlights the importance of considering cubic metres in warehouse design to maximise the use of available space.
What accounts, then, for the continuing emphasis on square metres rather than cubic metres?
The traditional method of measuring warehouse space in square metres may be due to groupthink, a longstanding way of thinking. However, the increasing use of automation in warehouses has caused some to rethink this method and consider the benefits of considering warehouse space in cubic metres.
By considering the cubic usage, companies may increase their utilisation by up to 50%, especially in Greenfield development.
Re-conceptualising warehouse builds in terms of cubic rather than square metres will change the way we design warehouses.
Despite the prevalence of the traditional process of purchasing industrial real estate land and then building a warehouse on that land, the rise of automation has initiated a shift towards more optimal warehouse design.
Some participants in the industrial real estate space may initially be hesitant to shift to a metric of measurement based on cubic metres rather than square metres in design. The overall incentives in the market strongly point towards the adoption of this new way of thinking, particularly where high levels of automation are incorporated in the operational specification of the facility.
This shift would allow increased efficiency and therefore enable greater utilisation of industrial land releases, in turn lowering prices and making it more accessible for businesses.
Overall, the shift to measuring industrial property in cubic metres would benefit all parties involved, resulting in more efficient use of land and lower costs for businesses. Landowners will derive more overall revenue, industrial real estate brokers will derive more revenue, and tenants will benefit from higher efficiency facilities delivering lower operating costs.
There are still barriers to adoption due to the risk-averse nature of key stakeholders and the long lifespan of industrial assets (more than 50 years).
However, companies with the ability to execute next generation designs will have a distinct advantage over their competitors. Their operational cost will be lower, and the building will be more efficient.
It may take some time for these concepts to become more widely accepted – as is the case with many innovations and ‘generational’ changes in thinking (slow uptake of solar in the industrial space is just one example) – but the potential increase in utilisation makes it worth considering for companies looking to optimise their warehouse operations. Eventually, this new way of thinking will become the norm.
Peter Jones