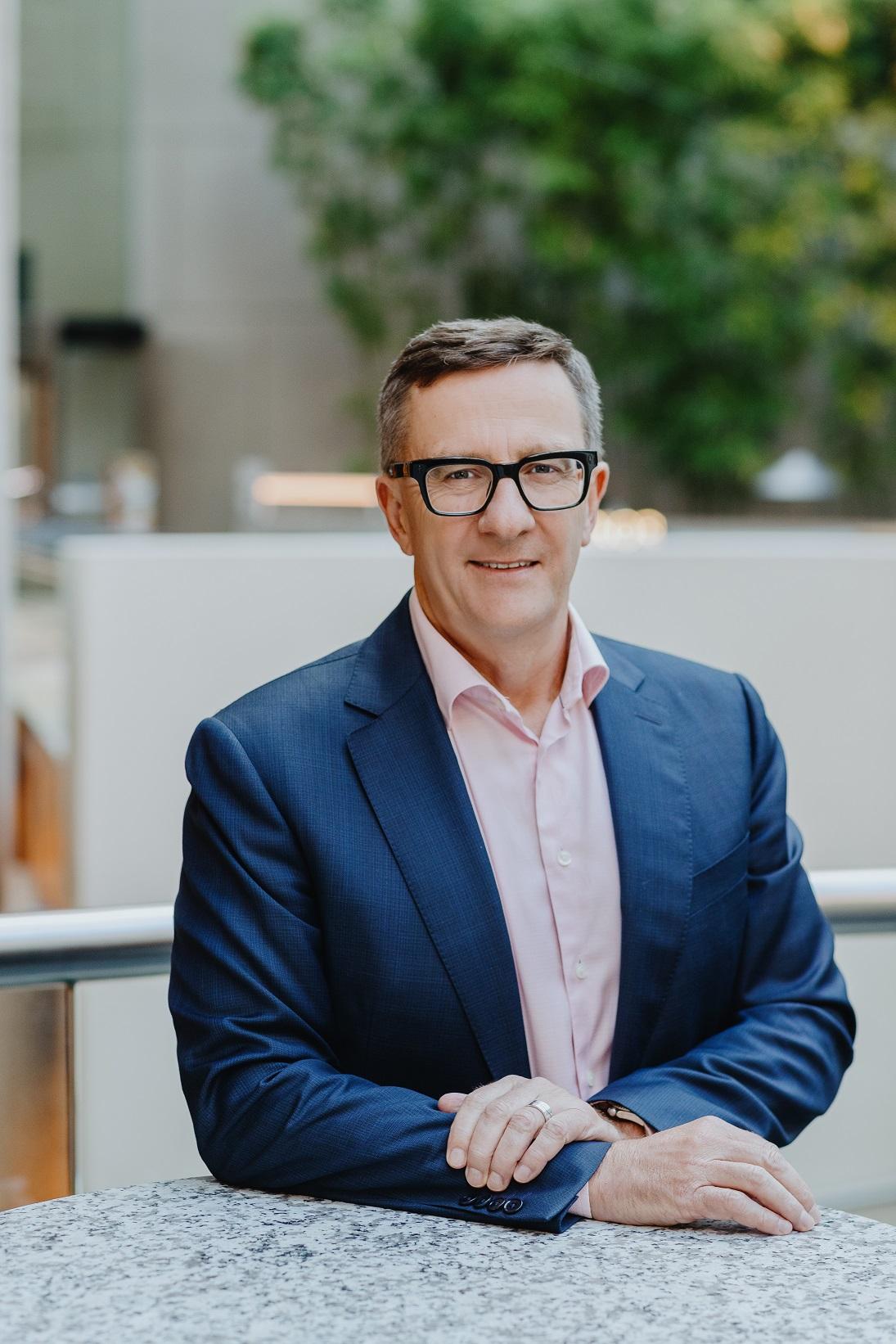
High construction costs throughout the Australian building industry have forced operators to seek new avenues to alleviate and manage the impact on their projects.
Construction costs within the building industry saw a dramatic increase during the pandemic, as a lack of building supplies saw shipping container costs from China to Australia reportedly rise to $12,000, up from a pre-pandemic price of some $2,500 to $3,000 per container.
Despite this, the real impact of the increase in building materials wasn’t felt until after the pandemic, as sub-contractors who were already committed to fixed price contracts with head construction contractors were unable to absorb the material price increases. This in turn resulted in some heavily leveraged contractors working on small margins going into administration.
Colliers Managing Director of Project Leaders, Jon Barnes commented that many of the strategies used to minimise costs involved detailed design management that examines the materials and the method of construction used in the project.
“Utilising materials that are readily available and have a secure cost point is one example of this. In addition, we are consistently looking at reducing on site construction times through the use of prefabricated building components or systems that reduce on site labour costs,” Mr Barnes said.
“The most fundamental way to reduce costs is to minimise the time spent on site. Working with construction contractors and architects, we aim to produce building designs that enable time efficiencies during construction.”
These methods can take many forms, including simplified building footprints and construction sequences to minimise material handling onsite, standardisation and prefabrication of façade elements to reduce construction times, as well as repetitive, standardised and simplified structural systems to enable quicker super structure construction times.
“The metrics are all around savings on construction contractor management costs or preliminaries as they’re known. With preliminaries running at approximately 18 per cent of construction costs, around $1.5 million a month can be saved on a $200 million project. If we can reduce the program by just two months, we can save $3 million,” Mr Barnes said.
“We have recently completed a major institutional project of over 25,000sqm where we worked with a tier one head contractor in Roberts Co to reduce the onsite time by some two months, employing some of these initiatives to achieve this.”
The sustained increase in costs following the pandemic is largely attributed to an increase in labour costs and the restriction of unskilled and skilled labour. In addition to this, Governments across Australia have continued to spend and invest on large scale infrastructure projects which has created a vacuum in the labour market. At current, construction costs are still 20 to 25 per cent above pre-pandemic levels.
“Given the existing and future ongoing spend by government on infrastructure projects over the next five years on projects such as the Commonwealth Games in Victoria, generational spend on hospitals in Queensland, education and health spend in NSW and transport infrastructure spend across all states, it is likely that pressure on construction costs will continue,” Mr Barnes said.
“It is clear that increased construction costs will not abate and that now more than ever principals, owners and developers will need to share the risk and work more closely with construction contractors to deliver projects. The one big upside to all of this is that it may bring the possibility of providing some equity of risk between construction contractors and principal owners.”